What does DPMO mean in Lean Six Sigma?
Defects-Per-Million-Opportunities, which is abbreviated as DPMO. It is also called as NPMO or Nonconformities per Million Opportunities. It is defined as the ratio of the number of defects in a sample to the total number of defect opportunities multiplied by 1 million. DPMO is a long-term measure of process performance. It is a measure of the error rate of a process. The metric tells you how good your process is towards committing mistakes. It requires you to think reversely.
Why DPMO?
Why is it necessary to calculate the DPMO of a process? It gives your business an accurate picture of the efficiency of your process. Depending on the Defects-per-Million-Opportunities, your company can decide whether it is necessary to launch a Six Sigma project that will improve the process and reduce the number of opportunities for defects per million products. If the DPMO is too high, you run the risk of negatively affecting customer satisfaction which in turn will reflect negatively on your business. Six Sigma business improvement projects focus on reducing errors and increasing customer satisfaction and thereby nurturing a healthy business. This is what does DPMO mean in Six Sigma approach.
Calculating DPMO:
1. The first step is to determine the total number of units to be sampled. In other words, you have to determine the sample group size. As a thumb rule, the sample size should be small enough to be manageable, yet large enough to reflect whatever problem is undermining the process.
2. The second step is to determine the number of defect opportunities per unit. That means, opportunities will have to be defined with the help of the following methods:
-
Creating a list of potential defects or errors per unit of process or product or service customers will care about
-
Focusing on places or process steps where something can go wrong and not on the ways it can go wrong
-
Focusing on routine, rather than rare defects or errors
-
Grouping or merging related or similar defects into one category
-
Going through this process, you have to keep the Voice of Customer in mind. Focus on the features that will impact on customer satisfaction and make sure that the traits are measurable.
3. The third step is to determine the total number of defect opportunities ONLY for the sample size under consideration. This is done by multiplying the number of units in the sample group with the number of defect opportunities per unit.
4. The fourth step is to count the defective opportunities within the sample group. You will simply have to calculate how many opportunities within the sample group actually contain defects or errors. It is important to take a sample group that is representative of the population. Also, the sample group must be large enough to be meaningful, but small enough to be manageable.
5. In the fifth and final step, we simply have to divide the total defects by the total opportunities which give us the DPO. Then we multiply the DPO by 1 million to obtain the Defects-per-Million-Opportunities. This value gives us an accurate, long-term, view of the efficiency of the process.
Source: Master of Project
FAQ'S
- What is DPMO in Lean Six Sigma?
DPMO (Defects-Per-Million-Opportunities) measures the number of defects per million opportunities in a process, helping to assess and improve process performance.
- What’s the difference between DPMO and DPU?
DPMO measures defects per million opportunities, while DPU (Defects Per Unit) measures the average number of defects per unit.
- How can I reduce DPMO?
Reduce DPMO by identifying defect root causes, using Lean Six Sigma tools, and implementing continuous process improvements.
- Why does DPMO affect customer satisfaction?
High DPMO indicates more defects, leading to lower product quality and customer dissatisfaction. Reducing DPMO improves quality and satisfaction.
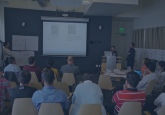
