The Key to Lean – Plan, Do, Check, Act!
Plan-Do-Check-Act (or PDCA) is one of the key elements in lean manufacturing, or for that matter in any kind of improvement process. In my view, it is the most basic framework for any kind of change. All other lean tools are only on top of the PDCA.
In our experience, most lean projects in the Western world fail not because they do not have some detailed tool, but because the PDCA is neglected. Of course, (almost) everybody knows what the PDCA is, but there is a huge difference between knowing the theory and doing it correctly.
Plan
The first step in the PDCA is the Plan. As the name says, you plan what you are going to do. Depending on the project, this may be the largest part of the effort of the PDCA. In fact, you can see it as a number of sub-steps or points that you have to address in the Plan. Depending on your progress, you may even have to do some of them iteratively until you get a suitable solution.
- Define the scope: What problem are you looking at?
- Define the target: What do you want to achieve? What are your goals?
- Analyze the situation: Try to understand what the current situation is. Talk to people. Visit the shop floor and observe (Genchi - Genbutsu). Collect data.
- Develop solutions: What approaches could help you to fix the problem?
- Select the best solution: Out of the different solution ideas, select which one you think is most promising with the biggest bang for your buck.
The Plan covers a lot of ground. Personally, if I would have to re-invent the PDCA, I would give it a few more letters beyond just plan. Oh, wait, people already did re-invent the PDCA, although I am not always convinced of the results (post with more details on PDCA variants coming up soon).
Do
This is the actual implementation. Change the shop floor, create the product, actually make it happen. In all likelihood, you will encounter additional problems during the Do that you did not think of before. That is normal. Just solve them as they come along.
In any case, try to make the Do stick. For example, if you change the way workers work, it is easy to have workers do it in a new way once. It is much more difficult to have them do it in a new way from now on. Depending on the problem you are trying to solve, standardization can really help here. Create a standard, train the workers, and confirm that they are following the standard even a few days later.
Check
This is probably the most frequently overlooked part of the PDCA. Did your implemented solution actually work? Did you achieve your goals? This is a very serious question. Judging from my experience, in most cases it does not, or at least not well enough.
Far too often, management is satisfied with a spiffy-looking presentation, and is ignorant of the reality on the shop floor. Additionally, they are also ignorant of the Hawthorne effect. This effect was first observed at the Hawthorne Works of Western Electric in 1930 and was named in 1950. In many cases, changing something on the shop floor will improve the system, regardless of what you change – but only for a short time! In other words, the management attention during a change process on the shop floor will lead to higher productivity and better quality, regardless of what is actually implemented. However, as soon as the management attention has moved on, everything reverts back to the old state.
This is a very common trap. You do a project, the KPIs improve, you move on, and the KPI then reverts to what it was. For an improvement project to work, the improvement not only has to actually work, but also has to continue working. That is the whole idea of the Check part in the PDCA.
Act
The Act is to decide what to do next. This depends on the outcome of the Check. If your implementation failed to achieve the targets, you have to find out the reason. Why did your solution fail to perform as you expected? This will lead to a repetition of the PDCA with another Plan to figure out a new or better solution to achieve your goals.
If you managed to achieve the goals (without falling back after two weeks, mind you!), you should congratulate your team and show your appreciation! With shop floor teams, I always had great success with a three-pound bucket of gummy bears or similar.
However, work never stops. Now you have to think about which problem to solve next. Prioritize your problems, pick the most relevant one (usually the one with the best-expected benefit for the effort), and start a new PDCA.
The PDCA repeats until the problem is solved.
Summary
Overall, the PDCA is for me the basic fundamental framework underneath all improvement activities. And I know it is not easy. I often find myself skipping steps or doing the PDCA sloppily if I do not pay attention. It takes a lot of focus and concentration to do it well. While the first two steps, Plan and Do, come naturally to most project managers, actually checking if it works and acting upon it is much rarer. I sometimes even have the feeling that the Check and Act are not really wanted in the industry. Pointing out that the newly installed immensely expensive equipment does not work is something not everybody wants to hear.
Source: All about Lean
Lean Reviews: Stories from Our Customers
Over the past 2 years, over 2,000 learners (2,197 to be exact) have come to DCM to learn more about lean and get certified. Read (and watch) their reviews to see how our courses have helped them achieve their career goals.
Course Overview
Our Lean Six Sigma courses provide in-depth training on FTY calculations and its importance in production processes, measuring the quality and efficiency of a process by evaluating the proportion of defect-free units produced. Our Lean Six Sigma courses equip professionals with the knowledge and tools needed to master FTY and drive continuous improvement in their organisations. Join us to learn from industry experts and take your career to the next level.
Membership, Stay Connected. Stay Relevant.
Completing a program is a point-in-time exercise that delivers huge value, but there is a next step to maintaining the currency of your skills in the ever-evolving professional world.
Membership is the next step.
A unique platform, membership is designed to ensure that you are in tune and up-to-date with the latest tools, trends and developments. Being a member provides just-in-time training and continuous professional development, and an exclusive and evolving content library informed by subject matter experts and industry leaders.
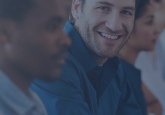